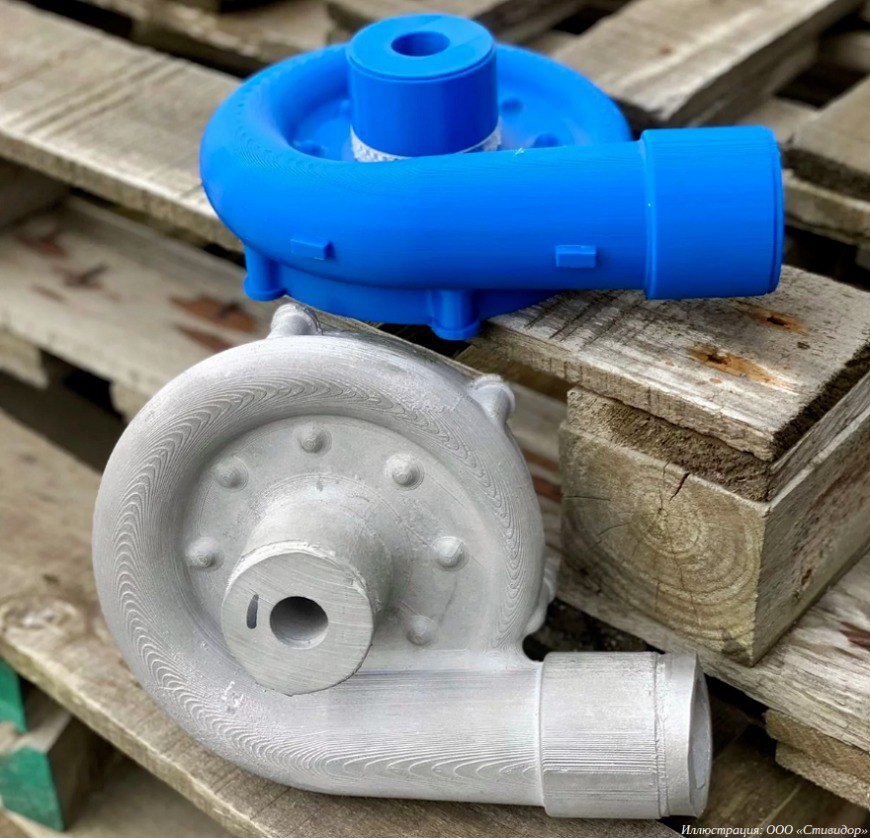
Подмосковный завод «Стивидор» использует ферму из ста пятидесяти FDM 3D-принтеров для 3D-печати выплавляемых мастер-моделей, по которым изготавливаются формы для отливки металлических деталей. Вкупе с обратным проектированием технология позволяет сокращать время производства более чем вдвое, а также выпускать малые партии серийных изделий, в том числе запчастей для импортного оборудования.
Изначально технология использовалась лишь как часть производственного процесса внутри предприятия, но современная потребность в импортозамещении позволила преобразовать инновацию в отдельное направление деятельности.
Особенно много заявок поступает на детали двигателей внутреннего сгорания, а также комплектующие промышленных холодильных систем. За 2022 год предприятие оцифровало более ста пятидесяти деталей и изготовило свыше десяти тысяч отливок. «Допустим, у вас есть некая шестеренка. Чертежей к ней нет, технической документации тоже. С помощью 3D-сканера мы сканируем деталь, далее в специальных программных комплексах создаем математическую модель. По сути, воссоздаем чертежи. При этом после реверс-инжиниринга документацию можно использовать не только в литье, но и в других производственных процессах — металлообработке, сборочных цехах», — рассказывает руководитель инженерного отдела Денис Пономаренко.
На основе цифровой модели, полученной 3D-сканером Scanform L5 и отредактированной в программе Geomagic Design, на 3D-принтере создается физическая модель изделия. Полимерную мастер-модель покрывают жаропрочным составом, а затем выплавляют, получая керамическую форму для отливки металлической детали — точной копии исходного изделия. Завод способен выпускать как единичные изделия, так и целые партии — для этого отдельной цех оборудован более чем ста пятьюдесятью 3D-принтерами.
«Нам присылают изделия, выработавшие свой ресурс, при этом часто деформированные. Детали не сказать, что сверхсложные, но отечественного локализованного производства лопаток, втулок, ступиц для таких рабочих колес нет», — поясняет Пономаренко.